Plastic Housing Manufacturers: Pioneers of Quality and Innovation
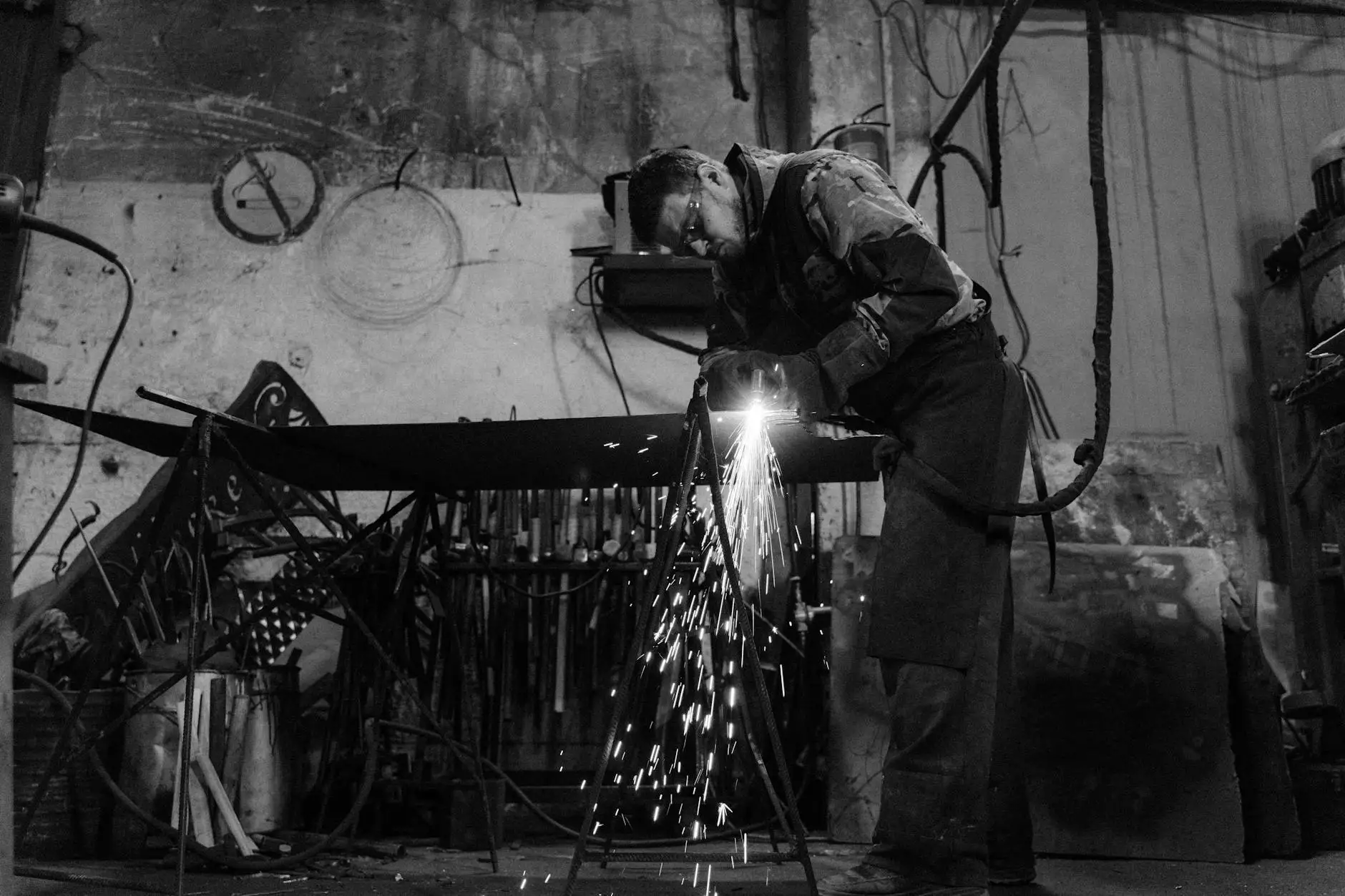
The plastic housing manufacturers sector plays a pivotal role in the global economy, providing essential components across multiple industries. From electronics and automotive to telecommunications and consumer goods, plastic housings offer a balance of durability, versatility, and cost-effectiveness. In this extensive article, we delve into the significance of plastic housing, explore the leading manufacturers, and examine the latest trends shaping the industry.
The Importance of Plastic Housings
Plastic housings serve several critical functions that enhance the usability and appeal of products:
- Protection: Plastic housings safeguard delicate components from environmental factors such as moisture, dust, and physical damage.
- Customization: The flexibility of plastic materials allows for extensive customization, enabling manufacturers to meet specific design and functional requirements.
- Lightweight: Compared to metals, plastics are significantly lighter, which contributes to reduced shipping costs and ease of handling.
- Cost-Effectiveness: The production process for plastic components is generally more affordable, making them a popular choice for mass production.
- Sustainability: New developments in biodegradable plastics and recycled materials are enhancing the environmental profile of plastic housing.
Key Players in the Plastic Housing Manufacturing Industry
Within the realm of plastic housing manufacturers, several companies stand out for their innovation, quality, and sustainability initiatives. One such company is Celtic Composites, a leading manufacturer based in the UK.
Celtic Composites: A Model of Excellence
Celtic Composites has made a name for itself by delivering high-quality plastic housings that meet the rigorous demands of modern manufacturing. Their commitment to excellence can be seen in several areas:
- Advanced Manufacturing Techniques: Employing state-of-the-art technology, Celtic Composites ensures precision and quality in its products.
- Research & Development: Continuous investment in R&D allows the company to innovate and improve existing products, ensuring they remain competitive.
- Customer-Centric Approach: They prioritize customer satisfaction by providing tailored solutions and exceptional support services.
- Sustainability Initiatives: Celtic Composites is committed to using eco-friendly materials and reducing waste in its manufacturing processes.
Trending Materials in Plastic Housing Manufacturing
The choice of material significantly impacts the performance and cost of plastic housings. The following materials are becoming increasingly popular among plastic housing manufacturers:
1. ABS (Acrylonitrile Butadiene Styrene)
ABS is a widely used thermoplastic known for its impact resistance and toughness, making it ideal for electronics, automotive components, and more. Its ability to be easily machined and molded contributes to its popularity in the industry.
2. Polycarbonate
Polycarbonate offers superior strength and optical clarity. Its resistance to heat and UV light makes it a preferred choice for outdoor applications, including automotive and electronic housings.
3. Polystyrene
This lightweight and rigid plastic is often used in packaging materials and in the manufacturing of consumer products. Its low cost and ease of production make it a staple material for many manufacturers.
4. Nylon
Nylon's excellent wear resistance and strength make it suitable for heavy-duty applications. It is often found in automotive housings and industrial components.
5. Biodegradable Plastics
With sustainability gaining importance, manufacturers are exploring biodegradable options that decompose over time, reducing environmental impact and aligning with green initiatives.
Technological Advancements in Plastic Housing Manufacturing
Technology plays an essential role in enhancing the quality and efficiency of plastic housing production. Here are some key advancements:
1. 3D Printing
3D printing technology allows for rapid prototyping and customization of plastic housings, enabling manufacturers to create complex designs that were previously unattainable. This technology reduces waste and shortens production time, making it an attractive option for many manufacturers.
2. Injection Molding Innovations
Advancements in injection molding technology have increased the precision and efficiency of producing plastic housings. Improved molds and processes have reduced cycle times and waste, resulting in both cost savings and higher quality outputs.
3. Smart Manufacturing
Integrating IoT (Internet of Things) and AI (Artificial Intelligence) into manufacturing processes allows for real-time monitoring and predictive maintenance, improving efficiency and reducing downtime.
4. Sustainable Production Processes
Manufacturers are increasingly adopting sustainable production processes to reduce their environmental footprint. This includes energy-efficient machinery and practices that minimize waste and utilize recycled materials.
The Future of Plastic Housing Manufacturers
The future for plastic housing manufacturers looks promising, driven by innovation, sustainability, and the ever-increasing demand for durable and versatile products. Industry trends include:
1. Emphasis on Sustainability
With consumers becoming more environmentally conscious, manufacturers are expected to prioritize sustainable practices, adopting eco-friendly materials and reducing emissions in their production processes.
2. Increased Customization
As competition grows, the demand for customized solutions will rise. Manufacturers will need to adapt to specific customer needs and preferences, pushing innovation in material and design.
3. Global Expansion
The demand for plastic housings is not limited to one market. Manufacturers are increasingly looking to expand globally, tapping into new markets and investing in local production facilities to reduce costs and lead times.
4. Collaboration and Partnerships
To stay competitive, manufacturers will look for partnerships with technology firms and research institutions to stay at the forefront of innovation and market trends.
Conclusion
Plastic housing manufacturers are integral to various industries, offering innovative, durable, and cost-effective solutions. Companies like Celtic Composites exemplify the best practices in the industry, combining quality with sustainable practices. As the demand for plastic housings continues to grow, these manufacturers are poised to lead the way in innovation and environmental responsibility.
In summary, the industry’s future hinges on the ability to adapt to changing consumer preferences, technological advances, and sustainability challenges. By staying ahead of these trends, plastic housing manufacturers can ensure they remain competitive and continue to meet the diverse needs of their customers.